3.4.4 New Technology and Other Options
Significant energy efficiency technologies that less than ten years ago were
thought too long-term to be considered in an assessment of fuel
economy potential through 2005 (NRC, 1992), are now available for purchase in
at least some OECD countries. The US Partnership for a New Generation of Vehicles
(PNGV), the European Car of Tomorrow and Japanese Advanced Clean
Energy Vehicle programmes have helped achieve these striking successes. In December
1997, a commercial hybrid electric vehicle was introduced in Japan, demonstrating
a near doubling of fuel economy over the Japanese driving cycle for measuring
fuel economy and emissions. In 1998, a practical, near zero-emission (considering
urban air pollutants) gasoline-powered passenger car was developed, and demonstrated.
This achievement established the possibility that modern emissions control technology,
combined with scientific fuel reformulation, might be able to achieve virtually
any desired level of tailpipe emissions at reasonable cost using conventional
fossil fuel resources. Emissions problems now limit the application of lean-burn
fuel economy technologies such as the automotive diesel engine. Advanced technologies
and cleaner fuels may achieve similar results for lean-burn gasoline and diesel
engines in the near future. Such advances in urban air pollutant emissions controls
for fossil fuel burning engines reduce the environmental incentives for curbing
fossil fuel use by road vehicles. Automotive fuel cells also realized order
of magnitude reductions in size and cost, and dramatic improvements in power
density. The status of these key technologies is reviewed below.
3.4.4.1 Hybrid Electric Vehicles
A hybrid electric vehicle combines an internal combustion engine or other fuelled
power source with an electric drivetrain and battery (or other electrical storage
device, e.g., an ultracapacitor). Potential efficiency gains involve: (1) recapture
of braking energy (with the motor used as generator and captured electricity
stored in the battery); (2) potential to downsize the engine, using the motor/battery
as power booster; (3) potential to avoid idling losses by turning off the engine
or storing unused power in the battery; and (4) increasing average engine efficiency
by using the storage and power capacity of the electric drivetrain to keep engine
operation away from low efficiency modes. Toyota recently introduced a sophisticated
hybrid subcompact auto, the Prius, in Japan and has since introduced a version
into the US market. Honda also began selling in model year 2000 its Insight
hybrid, a two seater. Ford, GM, Daimler/Chrysler and several others have hybrids
in advanced development. The most fuel-efficient hybrid designs can boost fuel
economy by as much as 50% at near-constant performance under average driving
conditions. The added complexity of the dual powertrain adds significantly to
the cost of hybrids, and this could hinder their initial market penetration
in countries with low fuel prices, unless policies are adopted to promote them.
Hybrids attain their greatest efficiency advantagepotentially greater
than 100%over conventional vehicles in slow stop-and-go traffic, so that
their first applications might be urban taxicabs, transit buses, and service
vehicles such as garbage trucks. An assessment of the potential for hybridization
to reduce energy consumption by medium-sized trucks in urban operations concluded
that reductions in l/100km of 23% to 63% could be attained, depending on truck
configuration and duty cycle (An et al., 2000).
Testing the Toyota Prius under a variety of driving conditions in Japan, Ishitani
et al.,(2000) found that the hybrid electric design gave 40%50% better
fuel economy at average speeds above 40 km/h, 70%90% better in city driving
at average speeds between 15 and 30 km/h and 100%140% better fuel economy
under highly congested conditions with average speeds below 10 km/h. Actual
efficiency improvements achieved by hybrids will depend on both design of the
vehicle and driving conditions. Much of the efficiency benefit of hybrids is
lost in long-distance, constant high-speed driving.
3.4.4.2 Lower Weight Structural Materials
Mass reduction via materials substitution is a potentially important strategy
for improving light-duty vehicle fuel economy, because it permits synergistic
reductions in engine size without loss of performance. The use of alternative
materials to reduce weight has been historically restrained by cost considerations,
manufacturing process technology barriers, and difficulty in meeting automotive
requirements for surface finish quality, predictable behaviour during crash
tests, or repairability. The past few years have seen significant developments
in space frame structures, advanced new manufacturing technology for plastics
and aluminium, and improved modelling techniques for evaluating deformability
and crash properties. Ford has displayed an advanced lightweight prototype that
is a mid-size car with a weight of only 900 kg, as compared to vehicles weighing
1450 kg today. Even if some of the more exotic weight-saving materials from
Fords prototype were discarded, a weight reduction of 30% or more appears
possible. With engine downsizing to maintain a constant ratio of kW/kg, this
should produce a 20% fuel economy improvement. Some aluminium-intensive luxury
cars have already been introduced (for example, the Audi A8 and the new Volkswagen
Lupo with 3l/100km consumption), and Ford is known to be considering the introduction
of such a vehicle in the mass market.
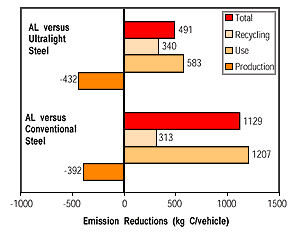
Figure 3.9: Life cycle CO2-equivalent greenhouse gas emission estimates for
automobile body materials.
|
According to Bouwman and Moll (1999), 85% of life cycle vehicle energy use
occurs in the vehicle use phase, with about 15% accounted for in vehicle production
and about 3% recovered in recycling. Mass reductions of 30% to 40% via extensive
substitution of aluminium for steel have been incorporated in the designs of
advanced, high fuel economy prototypes, improving fuel economy by 20% to 25%.
Because the production of aluminium requires more energy than production of
steel, and the recycling of aluminium auto bodies is more difficult given current
recycling technology, the benefits of substituting aluminium for steel must
be assessed by a life cycle analysis of greenhouse gas emissions (efforts are
being made to improve aluminium recycling technology, however). Analyses have
shown that accounting for life cycle impacts diminishes, but does not eliminate
GHG emission reductions caused by the use of aluminium for mass reduction in
motor vehicles (Figure 3.9). The amount of reduction, however, is sensitive
to several key assumptions. Considering the total life cycle emissions for a
typical passenger car in the USA, Das (2000) concluded that higher net emissions
in the production plus recycling stages would reduce the potential GHG benefits
of aluminium in the vehicle use stage by 6.5% versus conventional steel auto
bodies, but by 15.8% versus advanced, ultra-light steel body (ULSAB) designs.
Because the increased emissions come first in the production stage, there is
a recovery period before net emissions reductions are realized.
Das (2000) found a recovery period of four years versus steel but 10 years versus
ultra-light steel auto-bodies (ULSAB) for an aluminium-intensive vehicle. An
analysis by Clark (1999) of aluminium versus conventional steel, assuming fewer
lifetime kilometres, found a cross-over point at approximately eight years for
a single vehicle, but at 15 years for an expanding fleet of aluminium-intensive
vehicles. In comparison to ULSAB, the car fleet crossover point was found to
be at 33 years. In other OECD countries where lifetime vehicle kilometres may
be one-half, or less, the levels of the USA, the cross-over points would be
even farther in the future. Sensitivity analyses have shown that the results
depend strongly on key assumptions, especially the sources of energy for aluminium
production and lifetime vehicle miles.
Bouwman and Moll (1999) obtained similar results in scenarios based on the
growing Dutch passenger car fleet. A scenario in which aluminium vehicles were
introduced in 2000achieved lower energy use than a steel scenario after 2010.
By 2050, the aluminium scenario energy use was 17% below that of the all steel
scenario.
|