7.4.3. Future Development Paths for Aircraft Engines
Figure 7-12 provides a perspective on the future
based on historical trends. It complements the points made in Section
7.4.2 and relates to the fundamental thermodynamics of engines described
in Section 7.4.1. Figure
7-12 shows that the future path of engines with rising overall efficiency
requires improvements in thermal and propulsive (including transmission) efficiency.
In fact, relatively few options are possible for improving the propulsive efficiency
of current subsonic aircraft. Of these options, the most practical is to increase
the engine bypass ratio, which means enlarging the diameter of the propulsor.
Ducted propulsors with bypass ratios up to about 15 have been demonstrated,
but they incur drag and installation penalties. Bypass ratios above about 10
generally require the addition of a gearbox to the powertrain, but gearboxes
combining required high power capabilities, transmission efficiency, weight,
and long-life characteristics have yet to be demonstrated in service. Plans
for the introduction of such an engine (with a bypass ratio of 11) have recently
been announced, however. Above a bypass ratio of about 15, the duct must be
removed to contain weight and drag. Unducted propulsors resembling large, swept
propellers, with bypass ratios of more than 30, have been flight tested and
offer gains in propulsive efficiency of about 0.15 (i.e., a gain of about 25%)
compared to modern transport engines. These engines are labeled as "UDF" (unducted
fan) in Figure 7-12. Very high bypass ratio engines,
thus very large diameter (above 5-10 m) propulsors, are simply not feasible
for installation on existing aircraft because they do not fit within the dimensional
limits of the wing and landing gear. Thus, the application of large unducted
propulsors is restricted to new aircraft designs for which special accommodation
for the propulsion unit can be made. There would be additional costs to adapt
airport facilities to handle aircraft of markedly different layout resulting
from the use of very large diameter propulsors. Studies of aircraft with ductless
propulsors show that aircraft performance tends to optimize at flight speeds
5-10% below that of current transports as a result of aerodynamic efficiency
considerations. Community and passenger noise considerations of such engines
remain largely unresolved.
Studies suggest that propulsive efficiency could be further improved, by as
much as 5%, by integrating the propulsion system with the airframe to pass the
vehicle boundary layer through the propulsor (thereby canceling the airframe
wake). However, this approach would be practical only for very specialized,
all-new aircraft designs. Smaller gains (on the order of 1%) may be achieved
for a wider range of aircraft through more efficient mixing of propulsor and
core flows in the duct before the exit plane of the exhaust nozzle. This principle
has already been adopted for certain long-range aircraft for which extensive
research has been done to ensure that the weight and drag associated with the
mixer did not offset the gains in propulsive efficiency.
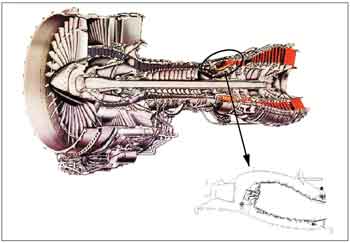
Figure 7-13: Engine cross-section and combustor detail.
|
Turning to the other option suggested by Figure 7-12-namely
thermal efficiency improvements-there are more technology opportunities that
can be pursued to effect overall efficiency improvement. These possibilities
can be grouped into improvements to current simple cycle bypass designs or new,
more complex engine cycles. Improvements to current approaches include the following:
- Further increases in the pressure ratio of compression systems
- Higher temperature hot sections with reduced (or eliminated) cooling requirements
- Improved component efficiencies.
Realization of any or all of the above improvements will require substantial
investments in a wide range of research and development fields, including aerodynamics,
cooling technology, materials, mechanical design, and engine control. Studies
suggest that total gains of 10-20% in the thermal efficiency of the engine might
be achievable by pursuing these options (Hill, 1996).
There are, of course, alternative or modified thermodynamic cycle approaches
to future engine design, such as incorporation of an inter-cooler and/or a recuperator.
Some of these technologies are used in land-based gas turbines, with large potential
gains in thermal efficiency. However, they invariably employ heat exchangers,
which increase engine weight to an extent that they are currently impractical
for aircraft applications.
There is a growing awareness, however, of the potential for reducing the weight
of aircraft engines by 20-40%. This general approach offers particular attractions
for application to long-range transport aircraft; as mentioned earlier, one
unit of engine weight generally saves between 1.5 and 4 units of aircraft empty
weight, with a concomitant decrease in fuel burn. Enabling technologies required
to achieve significant engine weight reductions include the following:
- Improved materials (composites and high-temperature materials in particular)
- Improved aerodynamics (to reduce the number of turbine and compressor stages)
- Increased turbine entry temperatures (to reduce airflow thus core engine
size required for a given power output).
None of these options is new to manufacturers, who already have research and
development programs addressing these subjects aimed at civil and military aircraft
of the future. As always, progress and success in meeting these objectives is
paced by the scale of investment by industry and/or government supporting the
work (a subject beyond the scope of this report).
The final question to be asked in reviewing future development paths for aircraft
propulsion is: Are there any serious alternatives to the gas turbine or derivatives
thereof as the primary source of propulsion for the aircraft of tomorrow? Several
other energy conversion technologies have been identified that may have potential
for application in commercial aircraft (e.g., solar power, nuclear power, battery/fuel
cell power, and hydrogen engines). However, these advanced concepts would require
major innovations, development, and changes in infrastructure before they could
serve as viable alternatives to hydrocarbon-powered gas turbine engines. We
cannot forecast when or if such developments will occur. Given the current state
of technology, there are simply no other energy conversion systems identified
to date that can offer competitive levels of thermal efficiency and power-to-weight
ratio for aircraft propulsion.
|