7.5.4. Reduction of Emissions
7.5.4.1. Earlier Developments
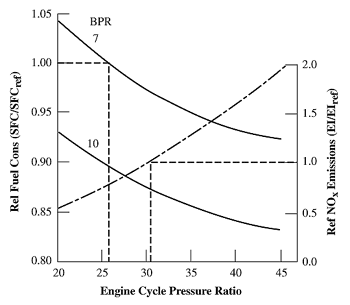
Figure 7-17: Effect of pressure ratio on NOx-specific
fuel
|
Between 1965 and 1975, low-smoke combustors were developed
and incorporated into low bypass ratio engines commonly used in early commercial
jet aircraft. These changes virtually eliminated visible smoke trails from aircraft.
Introduction of higher bypass ratio engines of the late 1960s and early 1970s-with
their significantly improved SFCs-marked a new and important step in reducing
CO2 and water vapor emissions from aircraft. These engines also emitted much
lower levels of HC and CO at low power ("idle") setting as a result of improved
fuel/air mixing and relatively high levels of pressure and temperature in the
combustor at this condition. Improved fuel/air mixing in annular combustors
of the new engines also reduced take-off smoke. The trend toward even higher
bypass engines, with their improved fuel efficiency, continues today, responding
not only to the initial and continuing commercial and operational pressures
but also to increasing concern about the effect of CO2 on the environment.
Between 1975 and 1985, new combustor design features that had better fuel atomization
and circumferential fuel staging at idle led to further reductions in HC and
CO emission levels. A typical example of such improvements in HC and CO emission
is presented in Table 7-3, which indicates the scale
of some of the benefits that have already been made toward abatement of urban
air pollution burdens (Bahr, 1992).
At that time, however, there was little change in the NOx levels; although,
as Table 7-3 shows, they were well within ICAO standards,
which applied to landing and take-off operations (ICAO, 1981). Emissions regulation
for HC, CO, and NOx are based on the total mass of each species produced over
the ICAO landing/take-off cycle, which is intended to represent typical aircraft
operations in the vicinity of the airport. The mass of each species (in grams)
is divided by the take-off thrust of the engine (in kilo Newtons) so that different
size engines can be reasonably compared; thus, the resulting units are g kN-1.
ICAO landing/take-off cycle, measurement procedures, and emissions standards
are discussed further in Section 7.7.1.
Table 7-4: Typical basic performance and operational requirements
of a modern aircraft engine combustor.
|
Item |
Requirement |
Value |
Max/Min |
1 |
Combustion efficiency
- At takeoff thrust (%)
- Idle thrust (%) |
99.9
99.0 |
(Min)
(Min) |
2 |
Low-pressure light-off capability (MPa) |
0.03 |
(Max) |
3 |
Lean blowout fuel/air ratio (at low engine power conditions) |
0.005 |
(Max) |
4 |
Ground light-off fuel/air ratio (with cold air, cold fuel) |
0.010 |
(Max) |
5 |
Total pressure drop-compressor exit to turbine inlet (%) |
5.0 |
(Max) |
6 |
Exit gas temperature distribution
- Pattern factor
- Profile factor |
0.25
0.11 |
(Max)
(Max) |
7 |
Combustion dynamics [dynamic pressure range/inlet air pressure (%)] |
3 |
(Max) |
8 |
Liner metal temperature (K) |
1120 |
(Max) |
9 |
Cyclic life to first repair (cycles) |
5000 |
(Min) |
|
Table 7-5: Combustion developments linked to emissions performance.
|
Requirements* |
Emissions Implications and Compromise Required |
1, 8, and 9
|
Lowering of liner cooling flows improves "idle" efficiency (low HC and
CO) and ability to reduce NOx but must be balanced against effect on liner
temperatures and life/durability |
2, 3, and 4 |
Wide range of fuel/air ratios and long dwell times in combustor favor
good light-off performance but must be balanced against need to control
HC and CO emissions at low power and NOx formation rates at high power |
5 and 7 |
Low overall and dynamic pressure losses required to minimize SFC losses
but must be balanced by need to retain good mixing for low emissions and
good liner cooling |
6 |
Long mixing lengths improve exit profiles and pattern factors but require
more cooling air and increase NOx formation times |
*See Table 7-4 for item requirement numbering
scheme. |
|