7.4. Engine Performance and Technology
For the past 50 years, the principal propulsion source for military and civil
aircraft has been the gas turbine. For a variety of technical reasons, this
situation is likely to continue into the foreseeable future. The earliest military
aircraft gas turbines, developed toward the end of World War II, opened the
way to high-speed flight by providing high power from low weight, compact engines.
For military use, these "jet" engines offered an escape from the aerodynamic
limitation of the propeller, despite their relatively low thermodynamic efficiency
at the time. Early civil aircraft gas turbines continued, at first, to use the
engine to drive a propeller in so-called turbo-prop form (engine shown in Figure
7-7a). Several types of turbo-props are still used for short-haul operations
where cruise speeds are less important, but larger and faster aircraft have
dispensed with the propeller.
Since those early days, huge strides have been made in the critical and pacing
technology fields that influence the key design and performance characteristics
of engine design. In particular, major advances have been made in the fields
of turbo-machinery aerodynamics, combustion, turbine blade cooling, and materials.
For military engines, these advances have been realized mainly in increases
in the ratio of engine thrust to engine weight. For civil aircraft engines,
the benefits have led to high bypass ratio engines with substantially lower
fuel consumption, which have contributed to the rapid growth in air transportation
over the past 3 decades.
It is common to compare engines in terms of specific fuel consumption (SFC),
which is the fuel flow rate per unit thrust at cruise. However, the ultimate
goal is to minimize total fuel burned per unit payload, rather than SFC; this
computation involves engine weight, installation drag, and their effect on the
total fuel required to complete a flight mission. For subsonic transport aircraft,
the weight of the engines is on the order of 10-15% of the empty weight of the
aircraft; a reduction of one unit of total engine weight translates to a reduction
of between 1.5 and 4 units of aircraft empty weight, depending on the design.
The relatively larger reduction in aircraft weight derives from concomitant
reductions in requirements for supporting structure. The benefits are further
magnified by the fact that the reduction in fuel burn attributable to engine
weight savings is proportional to increasing aircraft range.
The following subsections present a brief outline of engine performance issues
from an historical perspective (7.4.2) and a look
forward into the future (7.4.3). The link between performance
considerations and emissions is discussed in Section 7.4.4. Because the gas
turbine is expected to remain the principal power source for aircraft propulsion
well into the future, however, Section 7.4.1 presents
a simplified review of the engine's fundamental principles to explain, among
other things, why there is no reasonable alternative to the gas turbine or derivatives
thereof in the foreseeable future.
7.4.1. Fundamental Thermodynamics
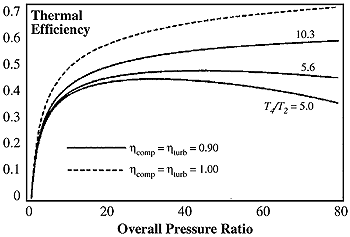
Figure 7-8: Gas turbine thermal efficiency. |
The core of the basic gas turbine consists of three essential elements: The
compressor, which mechanically increases the energy of the air (raising the
pressure and temperature); the combustor, in which fuel is burned (further raising
the temperature of the pressurized air); and the turbine, which mechanically
extracts enough energy from the hot compressed gas to drive the compressor (thereby
reducing the pressure and temperature of the gas). A fraction of the net energy
remaining in the gas after it leaves the turbine is then available to be used
in different ways, as shown in Figure 7-7. Case
(a) uses an additional turbine stage to mechanically convert the energy to shaft
work (such as might be required to drive a propeller or electric generator);
case (b) is the turbojet, in which a nozzle is used to accelerate the gas (converting
some of the energy into kinetic energy), producing a high-speed jet that can
be used to propel the vehicle; and case (c) is the turbofan, in which a further
turbine converts most of the energy of the gas into shaft work to drive the
bypass air compressor, thereby producing the bypass jet that propels the vehicle.
For aircraft applications, the weight of the engine must be low in relation
to the power output. This constraint has kept the aircraft type of gas turbine
simple-much simpler than those now being built for land-based power generation.
(The implications of going to more complicated configurations are considered
briefly in Section 7.4.4.)
The overall efficiency of an aircraft engine, h0,
is the mechanical power created by the thrust divided by the energy input rate of
the fuel flow. It is convenient to express overall efficiencies by
h0 = htherm x
hp, where htherm is
the thermal efficiency and hp is the propulsion efficiency; these terms are
considered below.
|