7.5. Combustion Technology
7.5.1. Introduction
Section 7.4 explained how major improvements in the fuel
efficiency of engines have been achieved through parallel advances in turbomachinery
aerodynamics, combustion, cooling, and materials. Significant progress in each
of these areas is the direct result of industrial and governmental investment
in balanced, interdependent research and technology programs that respond to
commercial and environmental pressures. This section focuses on combustion technology,
with particular emphasis on achievements to reduce emissions and the prospects
of further improvements.
We first describe the modern gas turbine combustion system and the particular
requirements placed upon this important engine component. Next we address emissions
from combustors. In view of the wide availability of excellent reference material
on this subject, however, only a brief assessment of the principal emissions
is given here. A new emphasis has been placed on current research aimed at improving
the understanding of soot formation and aerosols, a matter of increasing importance
(see Chapter 3). We then outline progress made in reducing
emissions in recent years. We go on to describe the specific part the combustor
plays in controlling NOx emissions from engines and discuss prospects and plans
for further improvements.
Table 7-2: Typical emission index (g/kg)
levels for engine operating regimes.
Species |
Idle |
Take-Off |
Cruise |
CO2 |
3160 |
3160 |
3160 |
H2O |
1230 |
1230 |
1230 |
CO |
25 (10-65) |
1 |
1-3.5 |
HC (as CH4) |
4 (0-12) |
0.5 |
0.2-1.3 |
NOx (as NO2)
|
|
|
|
- Short Haul
- Long Haul |
4.5 (3-6)
4.5 (3-6) |
32 (20-65)
27 (10-53) |
7.9-11.9
11.1-15.4 |
SOxO (as SO2) |
1.0 |
1.0 |
1.0 |
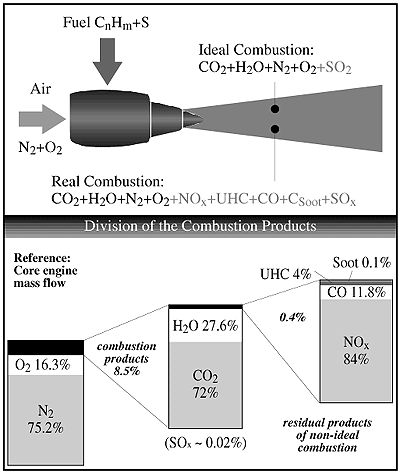
Figure 7-14: Schematic of ideal combustion products
(top),
and all existing combustion products, showing
|
7.5.2. The Gas Turbine Combustion System
In the cross-sectional drawing of a modern civil aircraft engine (Figure
7-13), the combustor is shown in its central position between the compressor
and turbine. High-pressure air enters the combustor at a relatively high velocity.
The air is first carefully decelerated to minimize pressure losses, then forced
into the combustion chamber, where fuel is added. The combustion chamber is
designed to allow time and space for the fuel and air to mix thoroughly and
burn efficiently before entering the turbine stages. Detailed design features
of the combustor control the complex burning processes, thus the completeness
of the chemical reactions involved and the nature and scale of individual emissions
from the engine. Therefore, the combustor has a key role in determining the
impact of aircraft on climate.
7.5.2.1. Combustor Features and Requirements
Aircraft engine combustors must meet the special requirements of operations
over a very wide range of pressures and temperatures. The combustor must be
able to ignite and accelerate the engine over a wide operational envelope. For
instance, it must be able to ignite at high altitude (up to 9 km) after an unscheduled
shutdown when the air is very cold (e.g., 220 K) and pressure is low (e.g.,
0.03 MPa). It must also be able to maintain stable burning over a very wide
range of air velocities and fuel/air ratios to prevent "flameout" during engine
deceleration. At the other end of the power range, when pressures and temperatures
are very high, the combustor must be able to burn fuel so that turbine components
are presented with a smooth temperature profile, to minimize damage to the blades
and vanes and thereby maximize service life. Together, these requirements present
a major engineering challenge because the simplest solutions to meet requirements
at one end of the operational envelope often conflict with those required at
the other. Relatively recent emissions requirements have added considerably
to the time and cost of developing combustors that fully satisfy the operational
and environmental requirements placed on today's aircraft.
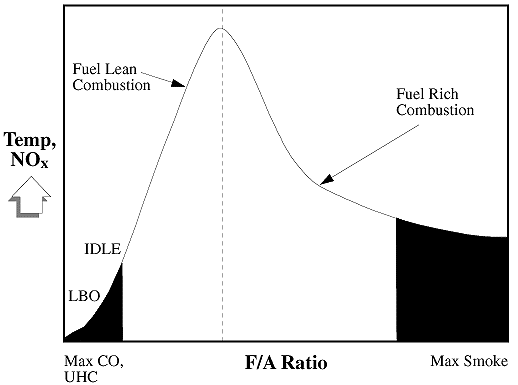
Figure 7-15: Fuel/air ratio dependence on NOx and temperature.
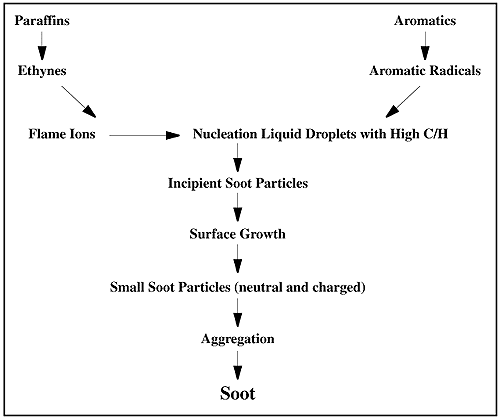
Figure 7-16: Schematic of soot production process.
|
Future combustors are likely to face even more challenging requirements as
manufacturers respond to the continuing need to increase fuel efficiency. As
explained in Section 7.4.1, higher cycle pressure
ratios lead to improved engine fuel efficiency. However, the compressor delivery/combustor
inlet air temperatures rise, reducing the cooling capacity of the air. A greater
proportion of total airflow is then needed to cool the hottest parts (liners,
blades, etc.). In turn, this requirement reduces airflow available for primary
combustion and dilution, making it more difficult to control turbine inlet temperature
profiles and emission levels. This cycle of primary and secondary problems,
which stem from increases in engine pressure ratios, can be broken only by continuously
improving the effectiveness of cooling techniques and devices and/or the use
of new and improved materials.
|